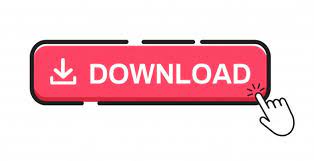
This has continued with the addition of five-axis control for machining between two curves, pencil machining and corner re-machining. The last few releases have seen the introduction of more five-axis toolpath capability into FeatureCAM. From 2013 onwards, you simply define the 3D models as “collision check” faces and the system will avoid them. In previous releases, the system required that you sketch out a boundary that defined an envelope around the part. Fixture avoidace in 2.5įixture avoidance has also been improved for 2.5 axis machining. This prevents toolpaths being generated in any areas where the benefit of the extra cut is negligible, such as cusps left by the previous toolpath. In addition, a new “detect material thicker than” command ensures that rest material thinner than the specified limit is ignored. New functionality eliminates excessive tool engagement and limits the maximum depth of any cut into un-machined material.Ĭollision checking against fixtures is easier and quickerīoth these controls reduce tool wear and improve surface finish by avoiding any overloading of the tool. Stock models are key to machining efficiently.
#Feature cam drawings zip#
The new “Send” command allows you to capture everything that relates to the job (parts, operations, libraries etc.), collect it together and zip it up into a single file that’s much easier to handle. There’s also a key change to how you can work with other team members and move data around. These are available for all machining operation types. These now extract information from the files and allow images to be taken for each set-up, as well as the finished part. Work has also been done on the set-up sheets that the system generates. Other general updates include changes to the tool library, which is now much more graphically rich, so you can pick the optimum cutter more quickly. All of the core operations and commands are immediately available and it’s pretty easy to dive in and get working. It’s now clean, fresh and sensibly laid out. If we start with the generally applicable updates to FeatureCAM, anyone with experience of previous versions will see that the company has been working hard on modernising the user interface. Its capabilities run the gamut of most production machining processes, from 2.5 to 5 axis milling, through tombstone, turning, mill/turn and into wire EDM. That’s the goal.Īlso, unlike some of Delcam’s better known applications for manufacturing, FeatureCAM (as you may guess from the name) is focussed on pulling geometric features from the CAD model (or indeed, sketch) and using that data to automate the toolpath creation process. Get the job, program the part, machine it and ship it. The typical use case is one where parts are low to medium in volume, not necessarily massively complex, which means that the bottleneck then becomes the toolpath programming process, rather than the machining itself. While the likes of PowerMill focus on surface quality for the mould and die market, and PartMaker concentrates on optimising toolpaths for large volumes of the same product, FeatureCAM is meant to be more general purpose. 5.If you’re not familiar with FeatureCAM, it differs from Delcam’s other CAM systems in that its goal is to provide the quickest route from getting CAD data (either as a drawing or a 3D model) to cutting on the machine. Now, draw a line in the same manner as you did in step 3 draw a curve starting at the point where the pencil tip of the compass meets the circle and draw inward until you get to the edge of the circle opposite to where you started. Rest the metal tip at the point where the curved line you just drew touches the outer circle. Now, draw a line in a similar manner as you did in step 1 draw a curve starting at the point where the pencil tip of the compass meets the circle and draw inward until you get to the edge of the circle opposite to where you started. Because this can be hard to understand, see the pictures above. Starting at the part of the circle the pencil part of the compass falls on, draw inward until the line gets to the part of the circle opposite to where you started. Turn the metal point of the compass so that the pencil it rests on the line of the circle. Place the metal point part of the compass at any point along the circle line.
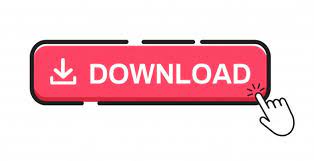